Laser Shaft Alignment
Know Better Alignment
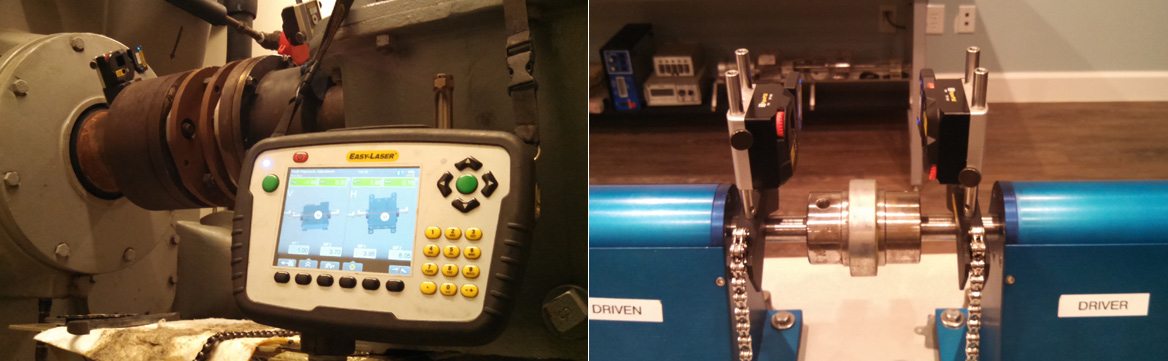
If you have motors, steam or gas turbines, pumps, gearboxes, compressors or any other rotating machines, precision alignment will have a positive impact on the operational life of the bearings, couplings, seals, shafts, etc and will reduce the power consumption of the system.
Utilizing the accuracy and quickness of state of the art laser measurement systems, shaft alignments can be measured, aligned and documented in record time.
Saves time and money for the company
You have much to gain in both time and money through having your machines aligned to the correct tolerances. An investment in having your rotating equipment aligned with a laser based alignment system rapidly pays for itself through lower costs for replacement parts, less downtime and smaller electricity bills. You get a better working environment into the bargain. Correctly aligned machines reduce the risk of expensive breakdowns and downtime. Typical problems arising from poor machine alignment are:
- Lost production time
- Leaking seals
- Increased vibration levels
- Higher energy consumption
- Bearing failure Shaft breakage
- Coupling wear
- Quality problems
Look to Integrated AVS for all your Laser Alignment Service needs.
OL2R Dynamic Alignment Measurements
OL2R or “off-line-to-running” measurements quickly and accurately measure the total change in rotating machinery alignment that results from thermal changes, dynamic machine loading, pipe strain, rotor torque, speed, etc.
The result is an accurate set of “Cold Alignment Targets” that will allow the machine or machine train to operate at optimal alignment under normal operating conditions. These measurements can typically be carried out in less than one day. Additional time may be required to properly align the machines following the data collection.
OL2R or “off-line-to-running” is a non-intrusive, safe and economical way to get the proper cold alignment target data.
OL2R Measurement on a Steam Turbine Driven Blower at a Steel Mill in the Midwest. Actual Alignment changes were completely different than the OEM recommended targets.
OL2R Measurement on a Solar Gas Turbine Driven Crude Oil Pump.
OEM Target:
Engine Low by 25 mils (Vertical Offset) Coupling open at the bottom by 0.8 mils/1”
Two identical Machines were measured. Actual changes were as follows:
Unit 1: Vertical Offset: -35 mils
Vertical Angularity: +0.4 mils/1”
Unit 2: Vertical Offset: -45 mils
Vertical angularity: +0.3 mils/1”
Note: "Identical Machines" do not exhibit "Identical" thermal growth characteristics.