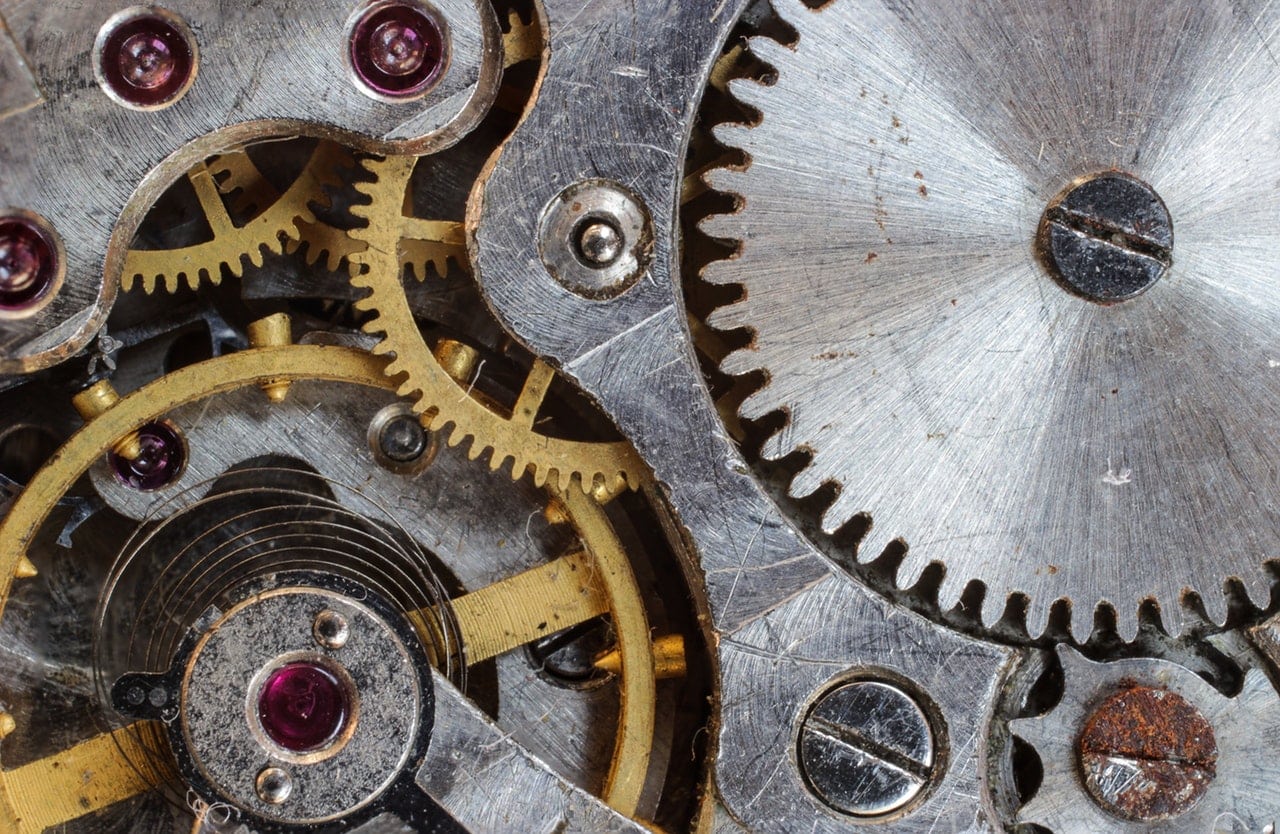
Basics of Vibration Analysis
August 30, 2019There are many nuances in the world of industrial maintenance. However, being proactive about the health of your equipment means understanding exactly what kind of maintenance will serve your needs best. In this post, we will detail the differences between alignment, vibration, and balancing. Each play a critical role in keeping your equipment working properly, so it is important to have an understanding of each.
Alignment
In rotating machinery, alignment is the center line coincidence of the rotating components, and the continuity of their angular alignment. Different components are related to each other by couplings, and couplings can be either rigid or flexible.
Rigid couplings require that components be perfectly aligned. Flexible couplings permit some error in either attribute. Some of these flexible couplings permit more offset (centerline coincidence error), while others permit more angular misalignment. Being familiar with the tolerances of the system, identifying the correct coupling, and using that context to align the components accordingly is crucial for rotating equipment.
Vibration
Spectrum Analyzer
Vibration is made up of the three basic physical properties of Motion, Velocity, and Acceleration. Vibration analysis is the observation and testing of random or cyclical movements of objects or systems and is very closely related to the study of sound waves. In industrial settings, technicians, engineers, and scientists quantify the three properties in Time Waveform and further define the spectrum using Fast Fourier Transform. By measuring and analyzing the properties using instruments and software, frequency results can be attributed to specific machinery or components. With today’s spectrum analyzers, very specific vibration signatures can be detected that point to particular bearing types, couplings, mounts, rotors and more. The most common use for vibration equipment is comparative analysis to baseline readings. Operators measure vibration of various machinery and components per a specific routine and detect changes in the behavior of the systems.
Balancing
Balancing Machine
Balancing is the act of making the effective mass of a rotating component statically and dynamically equal about its rotating axis. The Second Law of Thermodynamics states that objects in nature will always seek their lowest energy state. In the case of rotating machinery, if an offset exists between the center of mass and the center of rotation, the object will naturally want to fall (or rotate) to send the highest point of mass to the lowest point (closest to Earth) due to gravity. This essentially explains static balancing. Dynamic balancing is slightly different. Dynamic balance is defined as the state of equilibrium in which centrifugal forces due to a rotating mass do not produce force in the shaft. When an object rotates, centrifugal forces begin to take effect on the center of rotation. At very high speeds or as rotation accelerates, out of balance conditions can plastically deform the object as the point of high mass rotates past the point of highest gravity. When objects deform in motion, the out of balance conditions can lead to increased deformation and eventually failure by fatigue or even catastrophic failure by material yield. Analysis of dynamic unbalance is actually done by measuring vibration in a rotating system. Under specific conditions, an analyzer can pin-point the exact location of mass issues that can then be corrected by adding or subtracting weight.
Benefits of Working Together
Shaft Misalignment
Where the three collide is in the manifestation of the symptoms. Both unbalance and misalignment usually manifest themselves as vibration in the system. Dynamic unbalance induces vibration by the mechanism explained above, while misalignment results in vibration due to accelerations in out of alignment coupling components. The differentiation of the two can be challenging with common vibration analysis methods – however, it should be noted that unless components have been replaced, it is unlikely that their balance has changed. When a system is very large and complex with multiple rotating components, anchor points, dampers, actuators, neighboring equipment, etc., it is very challenging to pin-point root causes. In reliability engineering, one of the easiest aspects of a complex system to control is the alignment.
Eliminating the alignment as a potential source of vibration is relatively simple and effective. Shaft alignment technologies exist to make the simple coupling alignment a routine chore, while more sophisticated optical alignment methods or portable 3D metrology tooling is used for more complex systems. The benefits of alignment in rotary equipment include vibration reduction – resulting in less noise, increased energy efficiency, less component wear and a decrease of process related issues sparked by vibration.
Contact Us
You can Fill out a Form, Call, or Email to get in touch with Process Metrology, LLC to learn more about how we can help you.