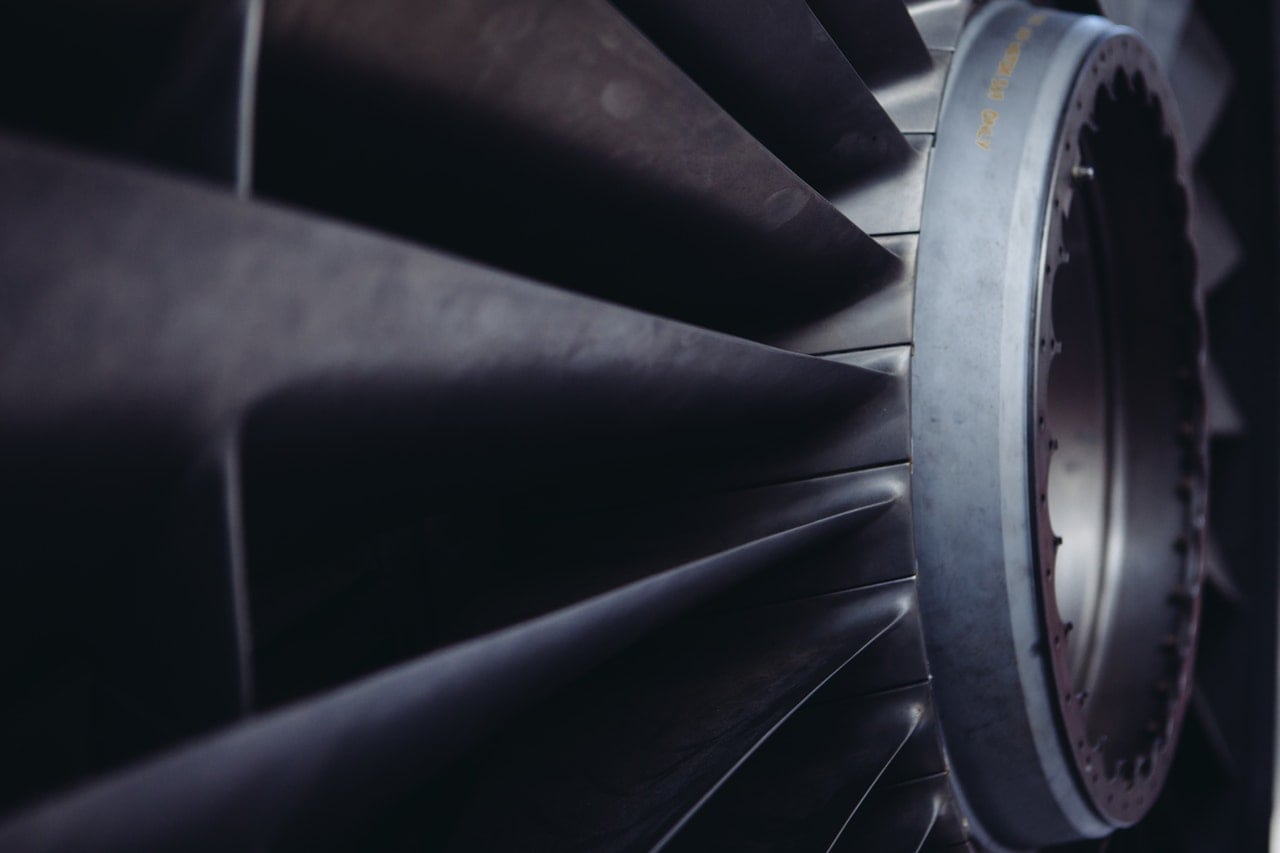
Reduce Costs and Downtime with Vibration Analysis
July 30, 2019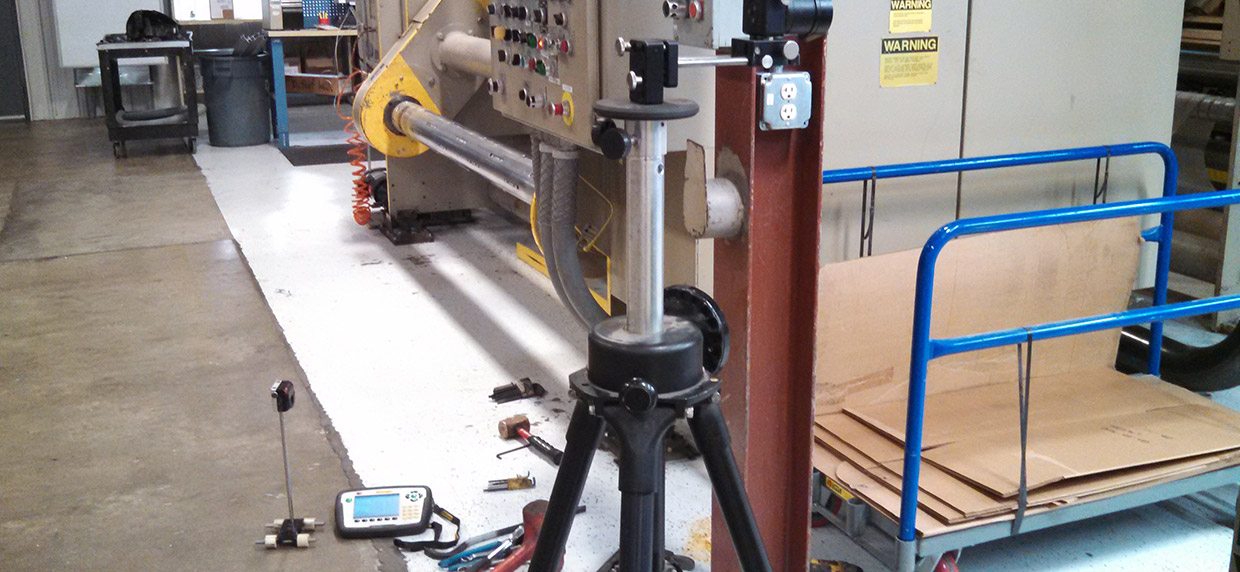
Alignment, Vibration, and Balancing Explained
October 24, 2019Maintenance is an important part of owning pretty much anything, but it’s especially important for machines with lots of moving parts. For many, this really only means making sure the machine is properly lubricated. However, there is another aspect of machine maintenance that gets far less attention: vibration analysis.
What is Vibration Analysis?
Vibration is simply the oscillation of something around an equilibrium point, and it’s unavoidable when dealing with machinery. Most of the time, vibration is perfectly normal and not a concern. However, as machines age, things go out of alignment, balance weights fall off, and parts bend and shift. In the end, these small problems come together and significantly impact the performance of a machine.
Vibration analysis uses advanced technology to determine the severity of a machine’s vibration, the effects on the machine if it continues, and what’s causing it.
Performing routine vibration analysis on a machine is like getting your car looked at every three months, and realigning and rebalancing your machines is like an oil change: it prevents small problems from turning into big ones.
What is The Process?
Many vibration analysis suppliers sell expensive analysis tools. While these are the tools necessary to complete the job, they are useless without the correct know-how and experience.
We, on the other hand, perform vibration analysis ourselves with our own professional tools. Our know-how comes included with the price of the analysis.
The gist of vibration analysis is that we have measuring tools that we attach to your machine. These tools are equipped with lasers that can detect even the smallest amount of vibration on your machine. These tools gather data while your machine is running, and our experts can provide an immediate diagnosis based on what the tools report. However, after that, we take the results back to our shop and do a more thorough analysis to determine what problems there are, if any, and what we can do about them. We use this data to properly realign your machine.
What are the benefits?
It Extends the Life of Machines
Vibration is a natural and expected consequence of machine aging. Machines are like humans in a way: as time goes on health and functionality is affected. Failing to perform vibration analysis is akin to refusing to maintain a car or take care of one’s body. All good things in life require care, and machines are no different. With proper, regular vibration analysis, you’ll ensure your machines live on to perform for many years to come.
Reduces amount of unscheduled downtime by 45%
It’s estimated that about half of unplanned machine downtime happens because of machine imbalance. Unplanned downtime is both stressful and costly, because it puts the entire production behind schedule and money is being lost by the second. In fact, not only is money being lost, but extra money has to be spent on repairs before production can even begin again! Essentially, regular vibration analysis is an investment that you’ll see a return on in the form of machine life, additional uptime and the remaining benefits listed.
Lowers energy bills
As a machine ages, it becomes less efficient. That’s true for two reasons.
- Over the lifespan of a machine, advances are made in technology that inevitably render the older technology less efficient. The newer version of a machine will almost always be more energy efficient than the older version.
- As a machine goes out of alignment, it experiences more friction and therefore must work harder to achieve the same results it did when it was aligned. This will increase electricity costs by thousands of dollars over the lifespan of the machine. Also, the harder the machine has to work, the sooner it will die out entirely.
Reduces the likelihood of breakdowns
Vibration will eventually destroy a machine beyond repair if left unchecked. Since factory machines often cost tens (or even hundreds) of thousands of dollars, vibration analysis works to protect your investment into your machines.
The case for prevention
Being proactive about potential problems and machine maintenance is the best choice 100% of the time. Choosing to spend a fixed sum yearly on maintenance is much, much better than just crossing your fingers and hoping that nothing breaks. Prevention is always cheaper than the cure. Here’s why:
- The costs never work out in favor of avoiding maintenance. You always lose the money you save by avoiding maintenance when it comes time to pay for repairs. That’s true even if you ignore the added costs of running a machine that becomes less efficient over time. Also, when assessing costs, you should factor in the money you would lose by being behind schedule after a machine unexpectedly goes down.
- The costs of unplanned downtime are inconsistent. The best advantage of maintenance over repair is that prevention cost is fixed—you always know how much you’re paying and what you’re getting. When you avoid maintenance, the following (and inevitable) repair cost could be low; or, it could be tremendously high and halt all production for days, resulting in hours upon hours of lost productivity—but you won’t know which until it happens. You should also take into account the extra stress you’ll experience when you decide to skip out on maintenance. If you’re in charge of maintenance, you’re going to get the blame when things break down.
Let Us Keep Your Machines Running Like New
If you’re sold on vibration analysis but aren’t sure where to start, give Process Metrology a call. We are experts who can get your machines running like new again in no time at all. Call us today for more information about how we can improve your manufacturing.